FLANGE IMMERSION HEATERS
Flange immersion heaters are designed for use in tanks and pressurized vessels to heat both gases and liquids. A flanged immersion heater will typically mate with a companion flange that is either welded to a tank or in the case of circulation heaters, to a pipe body. Flange heaters are designed to provide our customers with a long-lived, dependable, trouble-free heater for their application requirements. A properly designed flange heater will provide a high degree of efficiency as the energy that is generated is quickly dissipated directly into the medium that is being heated.
standard sizes:
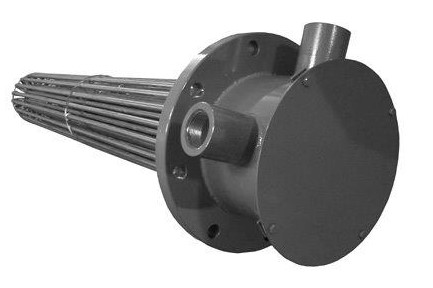
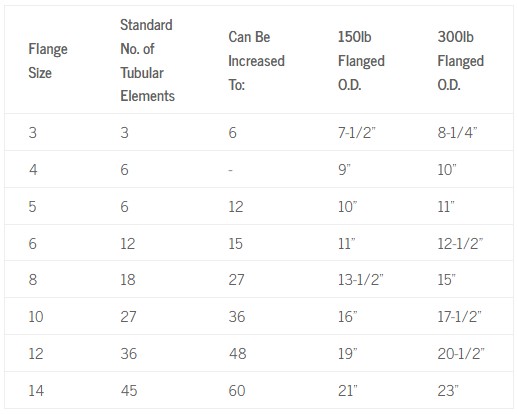
APPLICATIONS
COPPER SHEATH: Clean water, freeze protection, hot water storage, boiler and water heaters, cooling towers, heating of solutions not corrosive to copper
STEEL SHEATH: Asphalt, wax, paraffin, tar, fluid heat transfer mediums, petroleum, degreasing and solvent oils, fuel oils, machine oils, alcohol
STAINLESS STEEL SHEATH: Process water, soap and detergent solutions, soluble cutting oils, demineralized or deionized water (passivation recommended)
INCOLOY SHEATH: Solution water, corrosive solutions, air, gas, steam super heating
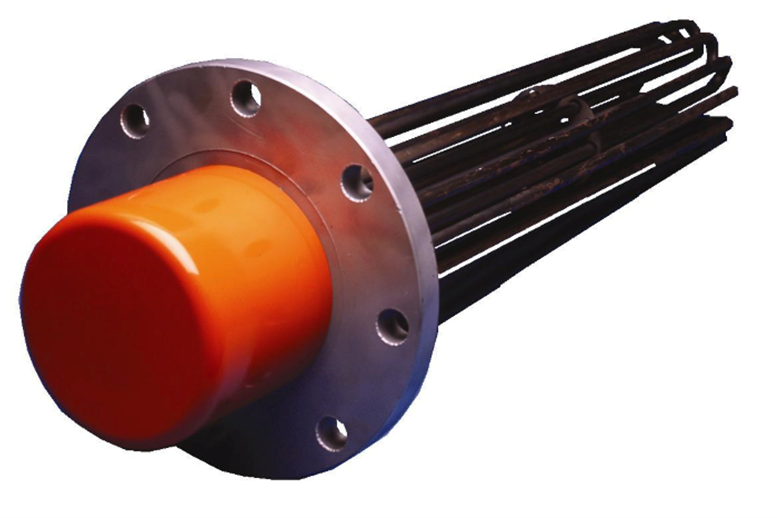
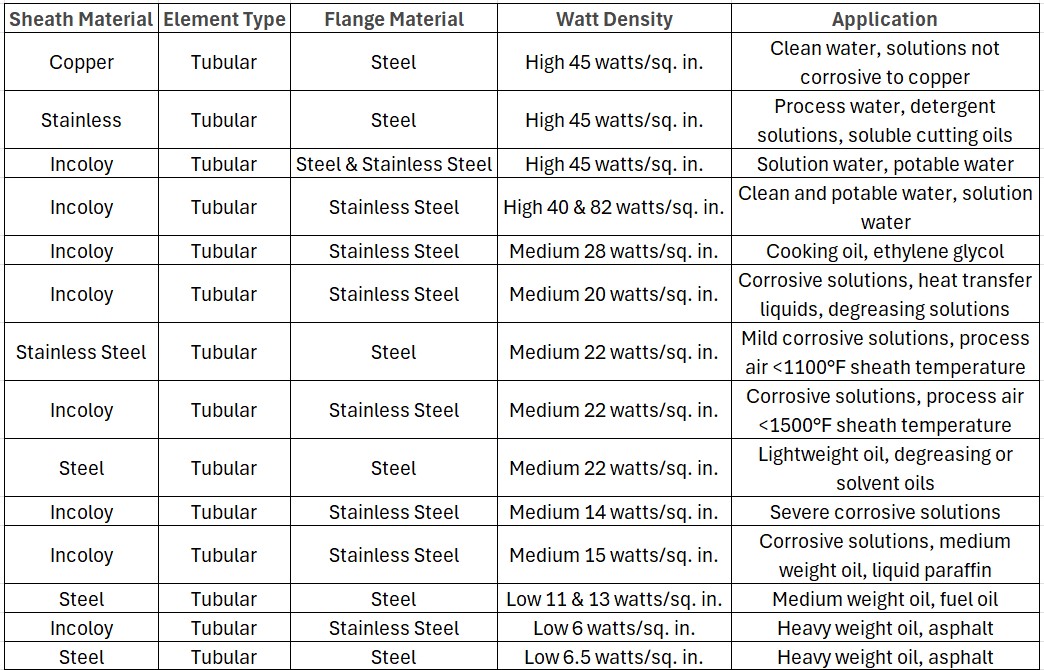
- UL & CSA Recognition on Elements.
- 334 stainless steel sheath standard on all items-allows for the widest coverage of applications and temperatures, plus gives a margin of safety should there be any unknown corrosives or contaminants in the solution.
- High purity MgO powder compacted to provide maximum heat conductivity and optimum dielectric strength.
- Type ‘A’ 80/20 resistance wire sized to provide lowest wire watt density for maximum life.
- Re-compacted bends to restore MgO density in bend areas.
- Moisture sealed to prevent the entrance of contaminants during storage and service. Silicone end seals on heaters for oil, air and corrosive applications. Epoxy seals for water applications.
- #10-32 terminals for wiring connections.
- Standard Nema 1 housings on all catalog items. Seamless deep drawn housings provide easy accessibility to wiring, plus afford a degree of protection to splashing or dripping liquids.
- Fixed conduit support bracket. Supply conduit is not disturbed when cover is removed.
- Welded construction between elements and flanges on steel and stainless steel headers to give maximum-corrosion protection and strength at elevated temperatures. All welds are hydrostatically pressure tested for leaks.
11. Silver braze construction on non ferrous flanges
12. Fusion welded junction between pin/resistance wire to provide a 360° circumferential joint, giving superior strength and life.
13. Spacer supports on units where immersed length exceeds 18″. This feature prevents adjacent elements from touching and overheating plus allows for easier assembly and disassembly from the mating flange.
14. ½ ” O.D. thermowells for existing or optional thermostats.
15. Standard flanges 150 Ib. rating ASA drill pattern ‘A6 raised face, other weights available.
16. Screw type lug line connectors for positive secure field connection points.
17. Optional MgO filled lnconel sheathed thermocouples welded to sheath. This feature provides positive sensing protection for over heat situations. Thermocouple junction location should be at area of highest operating temperature. (High Limit push to reset controllers available for thermocouple signal.
18. 100% inspected for:
– Dielectric or Hi-Pot between conductors and sheath
– Insulation resistance.
– Wattage.
– Hydrostatic pressure testing done on
steel and stainless steel flanges also
insures the sheath is defect free.
ADDITIONAL OPTIONS
- Nema 4 or 7 moisture or explosion resistant enclosures available on all flange sizes.
- Standoff housing design for high temperature applications.
Thermostatic controls in Nema 1, 4 or 7 enclosures available in (3) temperature ranges. - Thermocouples in either type J or K for control or high limit protection.
- Other sheath materials … Carpenter 20, Monel 400, lnconel 600, Hastelloy and Titanium.
- Type 304 or 316 stainless steel flanges.
- Passivated elements and flanges for pure and deionized water, photo chemicals and special processes.
Special lengths, wattages and voltages … consult factory.
watt density per application
- 90 Watts Per Square Inch – For heating clean water only in commercial and/or residential applications. Element life is sacrificed in favor of a low initial heater cost.
- 60 and 45 Watts Per Square Inch – Industrial water heating – many aqueous solutions which are compatible with steel and Incoloy.
- 23 and 20 Watts Per Square Inch – For heat transfer oil, cleaners, high temperature air and gas heating.
- 15 and 12 Watts Per Square Inch For lubricating oils, medium viscosity oils, high temperature air and gas heating.
- 8 and 6 Watts Per Square Inch – For #5 and #6 fuel oil heating, viscous materials, raw crude oil, residual oils, high temperature air and gas heating.
- 4 and 2 Watts Per Square Inch – For asphalt and other hard-to-heat substances, extra high temperature air and gas.